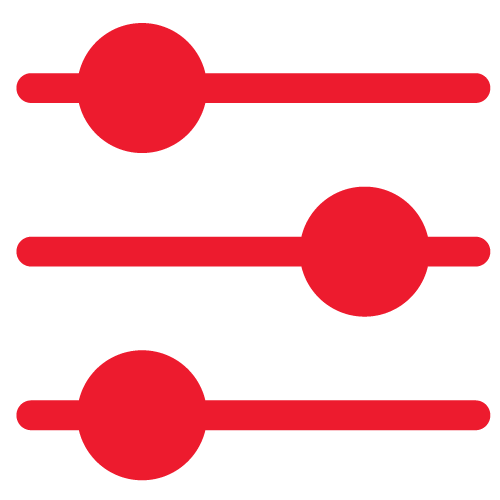
Custom Projects
Throughout the year’s we’ve designed, engineered and built many custom projects for our customers. Find out more about some of the problems we were able to solve by creating a custom solution, below.
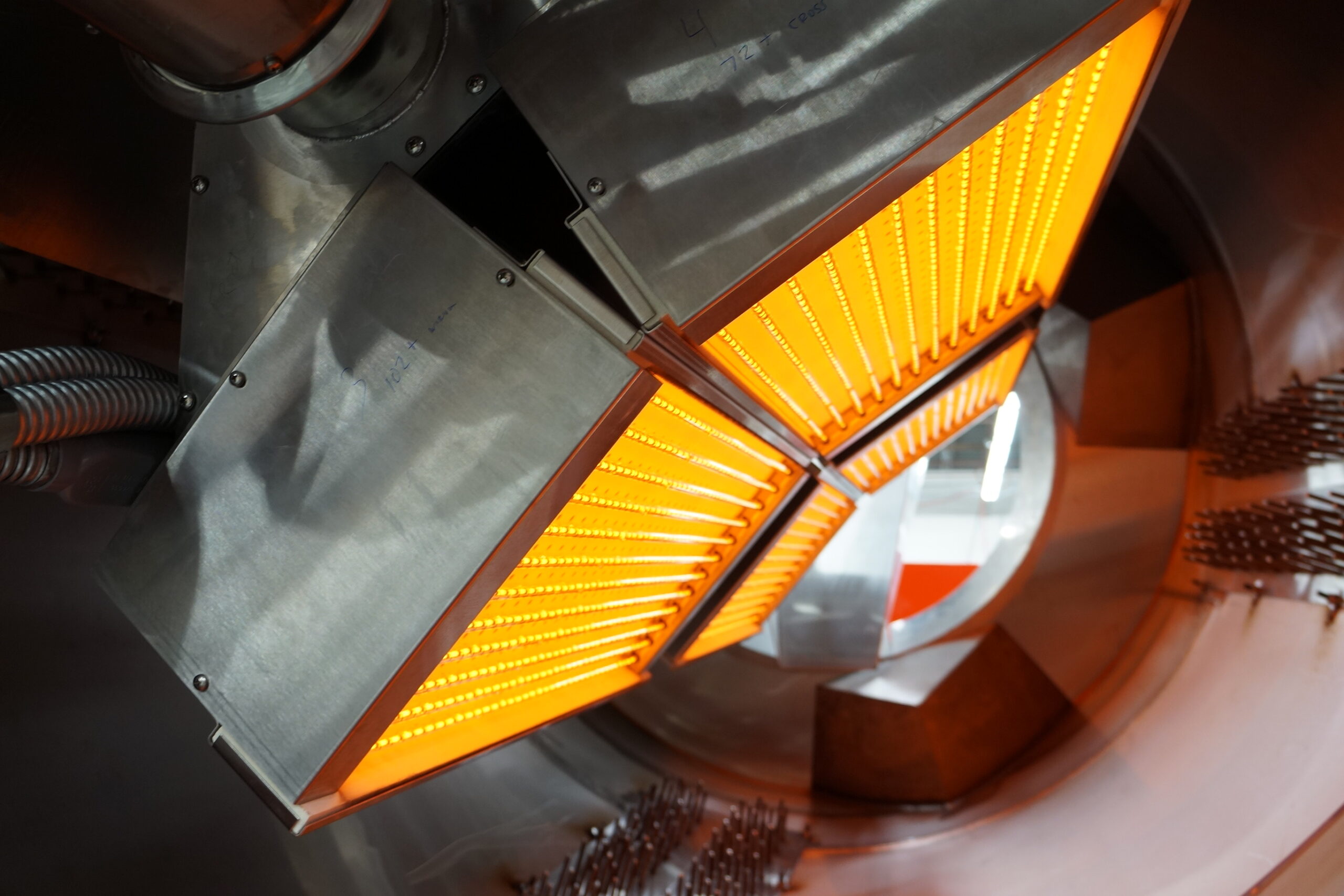
Biosolid Drum Dryer
Custom designed IR-8 infrared dryer drum and control system for drying biosolids and similar materials. Drying is performed by 4 IR heaters with a 25" heated length and 12" heated width, rated at 480V and 42.55 KW for 170.2 total KW. The 60" diameter drum dryer is equipped with tumbler plates and sits in a frame of extruded aluminum that is hinged to a welded steel base frame for tilting the drum dryer to discharge the material. The dryer frame is capped with exhaust hoods and a blower fan and wrapped in a stainless steel skin. A chute is attached at the loading end and a hopper at the discharge end to make for easy loading and unloading of material. The drum is spun by a drive motor attached via a chain and sprocket drive mechanism.
The control system is a three phase, 480V, 300A system for heating and logic control mounted and wired in a NEMA 12 enclosure. The system sets the heat level, dryer rotation speed, exhaust blower speed, and controls and monitors all functions of the process. A 5.7" color touch screen is used for operator control, process setup, and process data monitoring.
- 5.7″ color touch screen for operator control
- VFD’s for controlling the drum rotation speed and the exhaust blower speed
- NEMA 12 free standing enclosure
- Stainless steel safety skins
- Stainless steel drum, 60″ diameter x 78″ long
- Latching connectors on heater cables and junction box for ease of heater maintenance
- 5.7″ color touch screen for operator control
- VFD’s for controlling the drum rotation speed and the exhaust blower speed
- NEMA 12 free standing enclosure
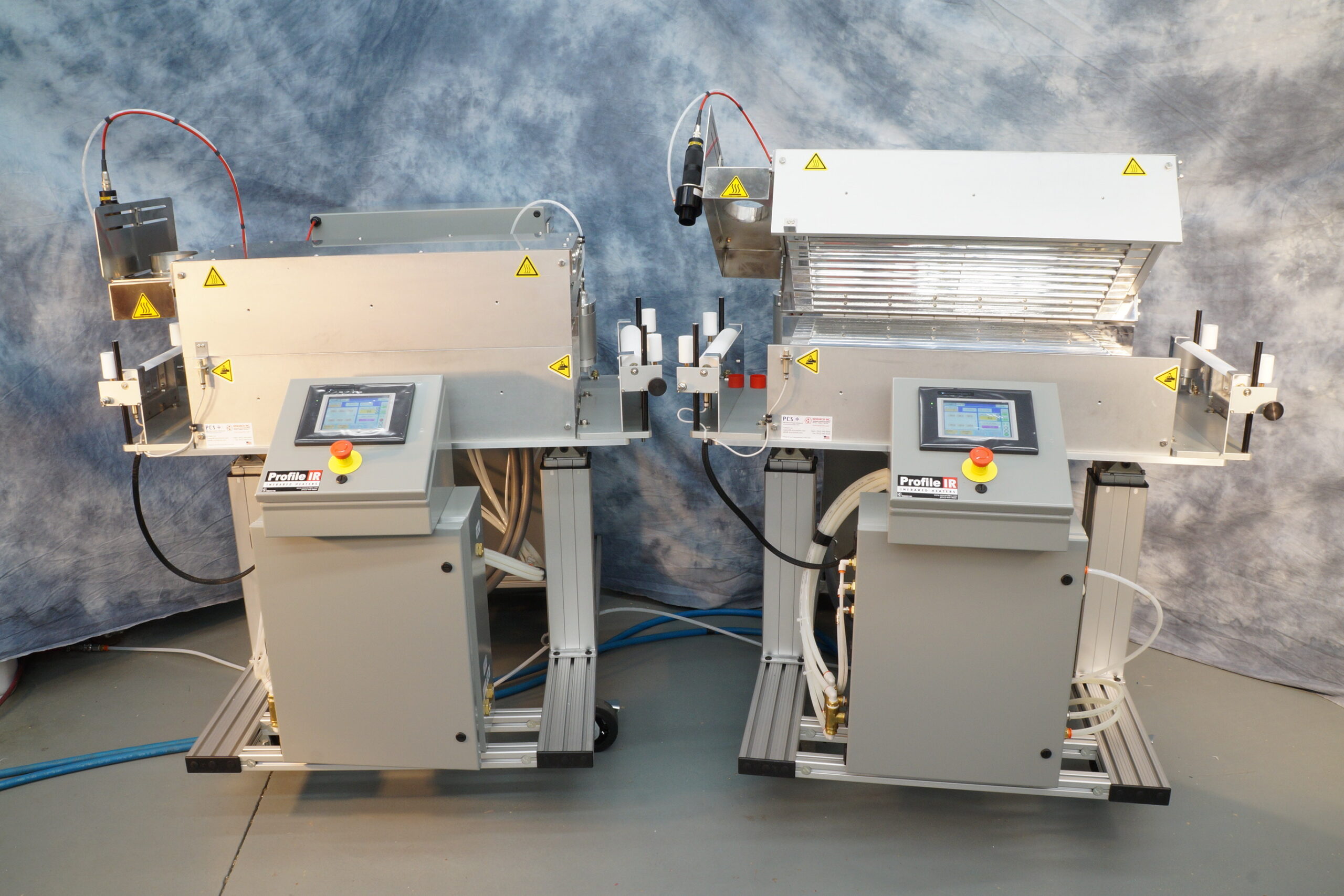
Multi Zone Industrial Chamber Heater Cart
The custom designed rectangular chamber curing system uses high intensity infrared lamps and polished aluminum reflectors to deliver heat precisely where it is needed for many curing and drying applications on extrusion lines. It can be used effectively to provide a surface cure to rubber extrusions, dry adhesives and coatings on rubber or metal, and provide in-process curing between layers of multi-layer cable. The heater is configured into six zones that provide defined heat intensities to match the profile of the product passing through the heater. Multiple recipes are provided to allow quick change-over from product to product.
The system includes a rectangular shaped ChamberIR heater with an opening that is 14" wide by 4" high, an operator interface pedestal with a color touch-screen display, height adjustment with plus/minus 15 degrees of tilt off horizontal, and convenient connection points for power, water, and air. The system also includes an optical pyrometer to monitor product temperature, product guides located on both the input and output ends of the chamber, product brake sensing to shut power down based on line speed, and an air nozzle kit to provide forced air inside the heating chamber to increase efficiencies in curing and drying or to provide rapid cooling in the event of a line stoppage.
- Rectangular chamber opening
- Hinged lid
- Product guides with adjustable height and width
- Industrial cart
- Built in cooling and exhaust
- Rectangular chamber opening, 14″ wide x 4″ high designed for flat product
- Heated area is 13.5″ wide x 25″ long
- 18 short wavelength T3 lamps mounted nine on the top and nine on the bottom
- Hinged lid operates with an air cylinder controlled by the operator display screen or remotely via a set of dry contacts
- 12″ wide product guides with adjustable height and width.
- Chamber is water-cooled and includes flow switch and thermostat switch for protection
- Cart is made with structural aluminum frame and 4″ wheels
- Allen Bradley PLC with color touch screen display mounted on the operator pedestal
- Six independently controlled heating zones
- 20 recipe storage capability
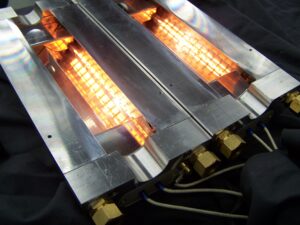
Water-cooled infrared heater to fit inside a 5 inch magnet
Custom designed water-cooled infrared (IR) heater to fit inside a 5 inch magnet. The IR heater has a 1.1 inch ID to accommodate customer supplied specimen tube. IR heater has 4 – 1000W short wavelength T3 lamps focused to the center of the chamber using polished aluminum elliptical reflectors.
IR heater can be operated with AC or DC voltage, each lamp is rated 1000W at 240 volts. The power supply for the IR heater should be design to operate the lamps overvoltage for greater heating potential. Water cooling rate: 1.0 gallon / minute. Electrical: two lamps wired in series lamp, 480 volts AC/DC or greater will drive lamps to full or greater output. 5kW @ 560 volts DC, 9 amps.
- High temp (1000C) specimen heater
- Specimen in a reduced oxygen atmosphere
- Non-metallic heater components required to operate inside a large magnet
- Heater (diameter) must fit inside a 5 inch ID space.
- Heater chamber with split clamshell configuration
- Four 1000w T3 short wavelength lamps were used with an elliptical reflector to focus the IR energy to the center of the chamber where the specimen is located
- The elliptical reflector are water-cooled aluminum with polished interior surfaces for best performance
- The chamber has a center 1 inch (25mm) opening to accommodate the specimen in a sealed quarts tube to control the atmosphere
- A DC power supply was selected for compatibility inside the magnetic field
- Special tooling was designed and used to create the reflector in the size required
- Ray tracing software was used optimize the reflector design and predict the target heat flux was sufficient to react the specimen temperature
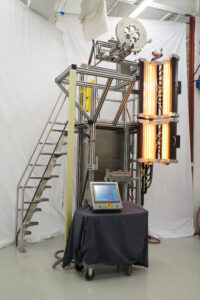
Vertical Silicone Cure Tower
Custom designed vertical silicone tube curing system utilizing two ChamberIR heaters mounted on an extruded aluminum frame. The system saves on floor space and maintains the tubing shape while preventing belt tracks and ensures high quality results. The tower supports inspection, treatment, printing, cutting, and spooling within the tower footprint.
- Accommodate silicone tubing sizes from .2″ to 3.5″
- Printer integration
- Cutter integration
- Turntable integration
- Non-contact tubing temperature measurement
- Support line speeds of 0 to 200 fpm
- Safety ladder access to threading platform
- Dual ChamberIR infrared heaters, up to 68KW per chamber
- Liquid cooled infrared heaters provide fast heat up and minimize fire risk on line stop with fast cooldown
- Heater ID up to 6.0″
- Heaters move up 10″ for cross-head maintenance access
- Extruded aluminum frame
- Adjustable capstan accommodates tubing from .2″ to 3.5″
- Integrated control system for heaters, capstan, and extruder interface
- VFD for controlling capstan speed
- X-ray/Laser inspection monitor and control